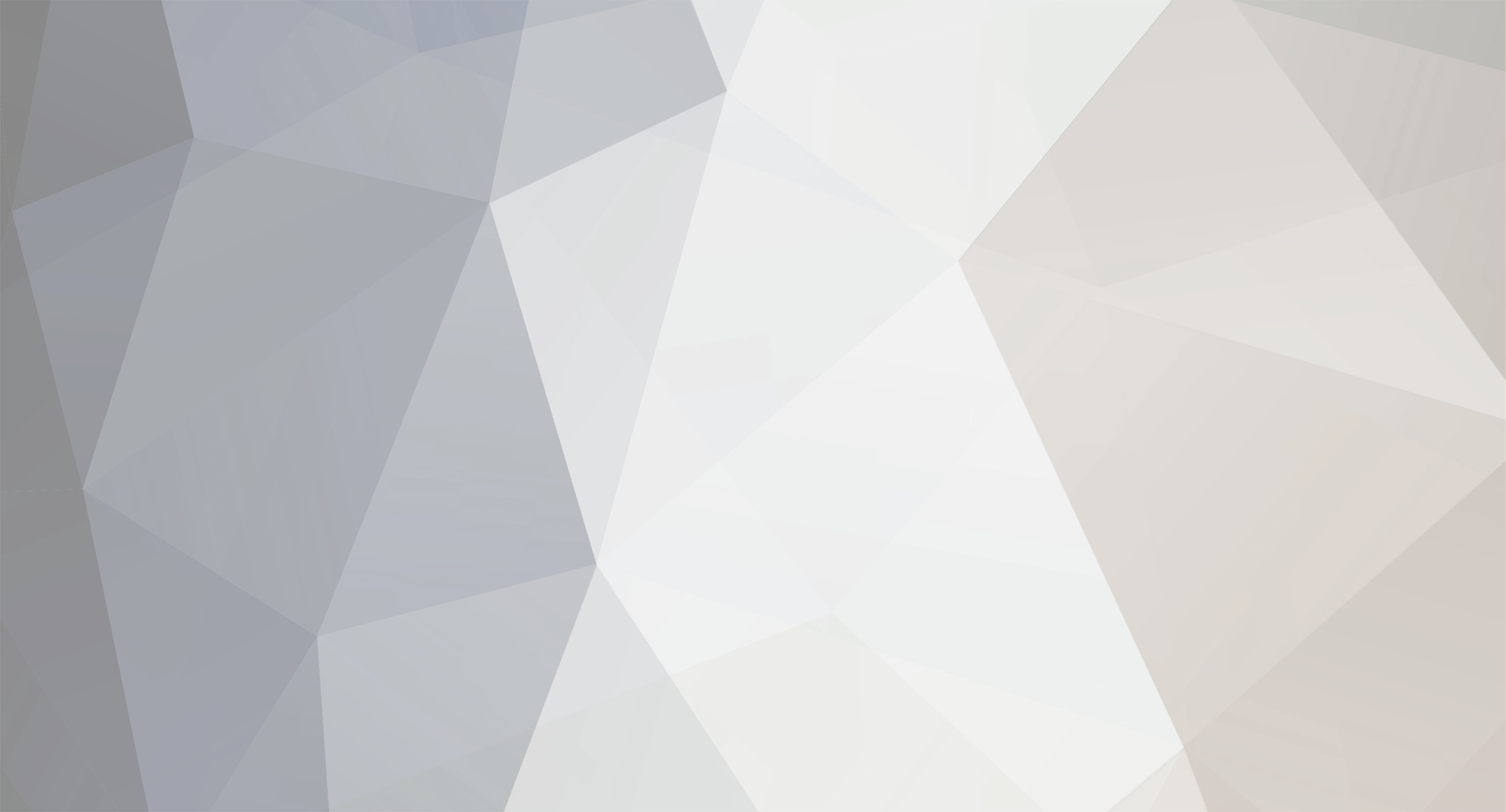
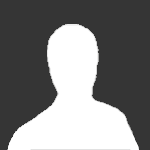
mslz22
Members-
Posts
1144 -
Joined
-
Last visited
Content Type
Profiles
Forums
Events
Gallery
Everything posted by mslz22
-
Hope to get back to this sometime this weekend. I made a mod of the arm cannons that i will share too. Decal art is done and will be getting my order into JT Graphics for the print out sheets. Reminder that i will forward that to everyone once i have it in hand. thanks mike
-
Agreed, on mine i used apoxie sculpt for the two rear doors on the front and the 2 rear doors on the back of each leg. I tried to use the included parts first but it was such a pain i abandoned those in favor of the apoxie sculpt. If your not familiar with apoxie sculpt it accepts scribe lines wonderfully and is easy to work with, non toxic too. mike Wonderful build here, you have some amazing patience!
-
Not too late, PM me or ordering info below. http://www.macrossworld.com/mwf/index.php?showtopic=41638 thanks mike
-
Bandai reissue 1/72nd regult with Mods/using as 1/100 which is what it
mslz22 replied to mslz22's topic in The Workshop!
It's somewhere in that neighborhood, it's something to play with a bit but how i do it is to wet a wide brush with some oderless mineral spirits, the load it with some of the oil paint, then start to brush it on a model, then dip the brush in OMS again and again until i get a nice even spread that is semi transparent. Too light and it won't stain the paint enough or deposit enough for shadows. That is for the filter/wash only, the color modulation is a much more delicate operation. -
More on how i got to this point soon, but did i mention this thing is massive. mike
-
Bandai reissue 1/72nd regult with Mods/using as 1/100 which is what it
mslz22 replied to mslz22's topic in The Workshop!
It's a process that you need to play with a bit to see what you like, some people wait overnight, i wait just about 4-5 hours. Part of it would depend on what you are using for thinner, the brand of oderless MS that i use is pretty dry after about 2 hrs. It's also important to make sure that the paint underneath is compatible and will not be eaten by the thinner. I use Tamiya acrylics so i have no issues. The idea is that the wash/filter, in this case anyway, gets into all the nooks in the flat paint, when you remove it you wind up added a sense of texture. You can remove as little as you want, but there is a limit to how much you can remove as it winds up "staining" the paint. They have a great line of oils, some of the blues are great for macross stuff, the regult, glaug, super armor etc. Those are not for wash/filters but for doing the color modulation as you can see a bit here in the nearly finished pics. That is done post wash, before gloss coat, then another touch up round after the decals etc are done. -
Yeah for that price i got 2!
-
Bandai reissue 1/72nd regult with Mods/using as 1/100 which is what it
mslz22 replied to mslz22's topic in The Workshop!
No look for it on ebay. It's Mig Productions oil paint. Starship Filth #502. They have a great selection of oils if you check out their page http://migproductionswebshop.com/index.php?cPath=25_97&osCsid=7cee2e956b654daf96321ae052cac60d I usually get them on ebay because they are out of the USA -
You can repeat that same operation with the other riser, this is one of the cases to ignore any alignment marks left from me making the pattern and just hold the parts in place, centered to each other and drill an alignment mark. This area on the left side has a bit of a gap, either from a bit of mold distortion or some other mystery resin issue. To address it, protect the back foot pad with some tamiya tape, then put a layer of petroleum jelly on just the tape. Add a bit of bondo or apoxie sculpt, I usually prefer apoxie sculpt but was in a rush today. Then squish the hole thing together, trim the filler and sand. Sorry about that, not sure why such a bad gap there, it's not on the pattern, I have a feeling the mold may get a bit over compressed when i bind it. It may vary from kit to kit if that is the case. Left main foot after alignment pins installed. Repeat the operations for the right side. Up next is to do a similar brass pin for the upper leg. Select an area in the middle of the leg strut that does not contain any rivet details and is in line with the appox middle of the contact area between the leg strut and the upper leg. Drill thru deep enough so that a 5/32 brass rod can used to firmly pin the upper leg and the strut. Then trim back the brass enough to fill the hole created by drilling thru. I use apoxie sculpt Main leg components held together with only pins, will be super strong when glued.
-
Make sure the bottom of the back foot pad is as flat as possible by sanding with a sanding block.. Drill holes in the mid foot plate, then hold centered upside down and drill thru to the main upper foot. This mid foot riser has only 1 pattern with some notching required by the toe to have it fit the left and right feet respectively. The taller side will go to the outside of the foot. Repeat that operation with the lower foot pad, and drill thru to the bottom of the foot. You can then put in some alignment rod, in this case 5/32 styrene. Put a dab of CA on the foot pad section only to hold in the rod, you will then be able to slide the 3 parts together and apart for more work. Trip back the rod when done.
-
Mods, hope it's ok to start a new thread for the instructions, lot going on in the old thread, just wanted the instructions and any discussions or ?'s separated out. thanks mike Ok, here we go, you don't have to do this in any particular order but i am starting at the bottom. First thing to note is that there are likely a few ways to approach this. My approach is to assemble the kit in such a way that almost everything can be separated out for ease of painting. Also note that none of the hardware is included in the kit. For the feet i am using 1/4 brass, 5/32 brass and 5/32 styrene (for location only). There are some location pins etc on most of the parts, these are there only to give you a starting point for aligning the parts. In some cases i will abandon those for various reasons and will note that when i do. First thing i want to do is get a sturdy connection between the upper foot and the main leg strut. Holding the parts together for alignment i first drill a pilot hole with a smaller size like 5/32, then work up to a 1/4 inch hole that passes thru the foot and into the strut. Be sure to drill in a location that is hidden by the part that i call the riser it's the transition part between the main upper foot and the back foot pad. There are 2 risers, one mentioned above and one mid foot
-
Bandai reissue 1/72nd regult with Mods/using as 1/100 which is what it
mslz22 replied to mslz22's topic in The Workshop!
Filter removed carefully after drying, ready for gloss coat, then decals, then more color filtering and modulation. thanks mike -
That's awesome, thanks for the link, wish the pics were a bit bigger.
-
Bandai reissue 1/72nd regult with Mods/using as 1/100 which is what it
mslz22 replied to mslz22's topic in The Workshop!
Thanks, yeah had used the apoxie sculpt to fill that in as well, again this will be fixed pose so if i need to adjust the ball at all i can still do it later on. So a little more progress over the last week, today is a snow day home with the kids so maybe i can sneak in a little more work. Hope you guys building this will find these tips helpful. One thing that needs addressing on the kit is the back door. I had to shave off the lip on the inside a bit and work on the fit. I used an elastic band to that apply clamping pressure to "pull" the door closer to the body. I used the orange cap tamiya glue to help fill some of the gap, and it's nice and sturdy since it's pretty much welded to the body. As you can tell by this pic, i painted the body and had a pretty bad result with the taping of this area, thus the wipe down and repaint. Even being careful and using magnified glasses the tape job and transition of this area still looked sloppy. I decided to etch a recessed panel all the way around this area. The sides were easy because i had a guide, but for the front i used drafters tape to establish the curve. It allowed me to get a much cleaner tape line, and i think it will look cool to have a clean panel distinction between these parts. One other neat little tip, for the back circle part of this, i found a plastruct dome that i used to mask off the area. Just a dab of hot glue to hold it down and it worked like a charm, much easier than masking a circle. Much better results than before And off the the downdraft table for the filter slurry. -
Using this as a 1/100, which is what IMO it really is. Long term plan is to do a few of these along with the 1/72dn glaug, which also is more like 1/100 IMO along with a few valks for a dio. I think these can look pretty cool with just a few mods and a good paint job. Part of why i am getting to do some of these now is my wifes schedule, every other week she works 4 nights in a row and i have a lot of time to watch the kids, won't work on anything messy upstairs, but these styrene kits are cool to kind of sit around, fiddle with, do the wetsanding etc. Key is to do the glue up a few days before, no glue up upstairs. In fact i have a downdraft table with a 4 inch vent that i do my glue ups on, even the Tamiya orange cap styrene glue gives off almost no fumes, it's really cool, and safe. So few of the mods that anyone else who is building this may like to take a look at. 1. Disregard all the stock joints and replace with aluminum or brass rod. This only works if you plan on doing a static model, which IMO is the best for this old guys. 2. Fill the joint slots with apoxie sculpt, looks better and sturdy for the brass. ] 3. Cut the hip joint, angled up, reinforces with a 5/32 brass rod thru. One of the problems with this kit, IMO, was that it always kind of looked like it had to use the bathroom with the hips so close in. 4 Add a spacer to the body to hip drive unit to accommodate the new wider stance with the hip mod. I'll add some detail to that part. And a few others that i may not remember at the moment. Long term project so it's a slow burn. Thanks mike .
-
That's awesome, and one of the fastest builds of a new kit, I would not be surprised if anticipated the parts breakdown and got a head start using a super battroid and super fighter kit for the armor/legs/arms etc. Then just finish up the parts from the new sprues. I do love the new gerwalk kit
-
This weekend, just wanted to be really sure that all was well with the stability of this, it's been attached for a while now so feel confident in it. Will start a FS thread on Friday.
-
Calling this finished, 1/48 with my resin launch arm and base. I went light on the decals, omitting most of them in favor of maintaining a more animie look. Pilot giving the thumbs up is a casting of the USV Club M pilot. thanks mike
-
Finished, pretty pics as soon as i can. thanks mike
-
Instructions will start sometime after the 1rst of the year, waiting on the decal file. Sorry for the lag in response, kids have been sick for 2 weeks (one after the other), and now are home for almost 2 weeks for the holiday, amazing how fast a month can get diced up. mike
-
The receiving unit of the launch arm is threaded, so mounting the valk is just a matter of "tightening" the bolt into the threaded receiver. You will be able to incrementally check the height/position of the valk by temporary mounting the boosters. They don't need to be permanently attached at this point. In fact it is very important NOT to mount the boosters permanently until the valk is in the correct position. You will not be able to get the boosters under the launch arm correctly otherwise.
-
Forgot to mention, you can change the angle of the launch arm in relation to the base by trimming the "mount" to the angle you want. It comes fully extended, but a trim will change the angle.
-
The great thing about the 1/48 kit is that it's set up component wise in a way that is pretty friendly to the launch arm. When mounting the valk, you only need this assembly to mount onto the launch arm, the rest will be added on later.
-
Getting close. Just a few LED's I had laying around to get the lights started.... Monstar run is just about done so i can start to get these going now.
-
Just got the weapons set today so i will be looking to finish this very soon. I actually needed to finish up the monster run to make time to cast these as well, only 2 or 3 more of those need to ship so hope to have time very soon. thanks mike